Tolerance rings can save your design when mounting ball bearings.
Tolerance rings can secure and mount ball bearings within housings or to shafts by exerting radial holding forces. A series of equally spaced waves or corrugations formed into their circumference act as springs to retain ball bearings in place. The amount of compression of these waves, the inherent properties of a particular tolerance ring configuration, and the properties of the mating surfaces determine the holding force strength.
Read more below on how tolerance rings compare to a press fit and can save your design when mounting ball bearings.
Retaining Ball Bearings Through Thermal Expansion & Contraction
Retaining a ball bearing can be difficult when wide service temperature ranges are encountered, especially with aluminum, magnesium or plastic housings. Unless the housing material has a coefficient of thermal expansion similar to that of the ball bearing races, a typical press fit or a slip fit at room temperature can loosen at higher temperatures.
The amount of retention force loss is further exacerbated with increasing ball bearing diameters. This problem results first in outer race slippage, then eventual destruction of the ball bearing and component surfaces. Components are the inner and outer cylindrical parts in which the tolerance ring is sandwiched between the shaft and/or the bearing.
Tolerance rings are made in three varieties: AN, ANL, and BN, each with specific properties and strengths for different applications.
AN TYPE
AN rings have corrugations that face inward. They are designed to fit outside a nominal circumference
BN TYPE
BN rings feature corrugations that face outward. Their rings are cut to fit inside a nominal circumference.
ANL TYPE
ANL rings are light-duty versions of AN rings with made with very thin material that do not maintain a circular shape in their free state.
The graph below illustrates tolerance ring performance in retaining a 6205 ball bearing (about a 2.00” OD) in an aluminum housing. With a 0.0012” interference fit, an installation force of 500 pounds is required. Due to thermal growth between the steel bearing and aluminum housing, the bearing becomes loose at a temperature of 170°F. With the tolerance ring, an initial installation force of only 320 pounds is required, and axial retention remains high at 230 pounds around 270°F.
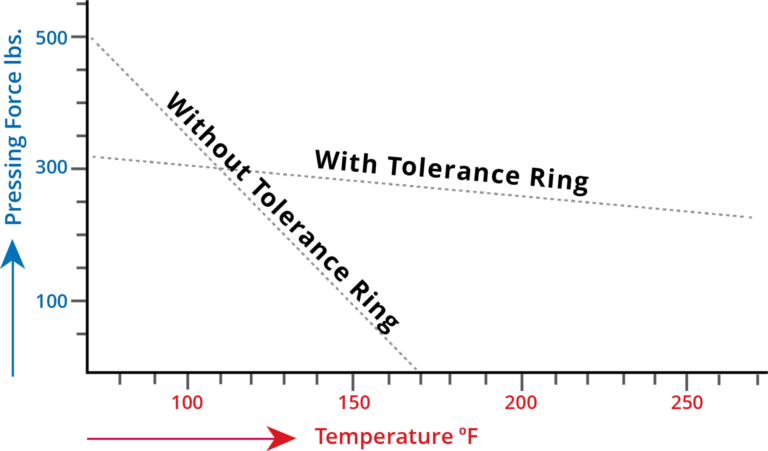
Reducing Ball Bearing Housing Tolerances
With a press fit of ball bearings upon steel components, achieving the tight tolerances of a few ten thousandths of an inch (0.0001”) on mating components (i.e., shaft, housing) can be costly, especially when ground finished surfaces are required.
Implementing tolerance rings allows for the relaxing of component diametric tolerances to a few thousands of an inch (0.001”). Often, the tolerances can be relaxed by a factor of ten when requirements go from a ground surface to a machined surface. In housings containing small nicks, dents or burrs, a tolerance ring provides an overlaying surface that compensates for finish irregularities. Relaxing tolerances through the use of tolerance rings can result in reduced component production costs.
Increasing Radial Loads on Ball Bearing Applications
For typical ball bearing applications, the radial capacity, or the maximum radial load that a tolerance ring can handle before yielding, is considered constant for a given configuration, provided the waves remain within their elastic range.
The configuration plays a critical role in how tolerance rings work, as it refers to the ring’s tolerance properties, such as diameter, raw material thickness, and pitch, or the distance between the wave peaks and valleys.
Depending on the amount of initial wave compression and if the waves are still within their elastic limits, there may be some movement away from the center when a radial force is applied. The loading point at which movement occurs can be adjusted and is directly related to the tolerance ring’s spring rate, the amount of initial wave compression induced at assembly, and the magnitude of the applied radial load.
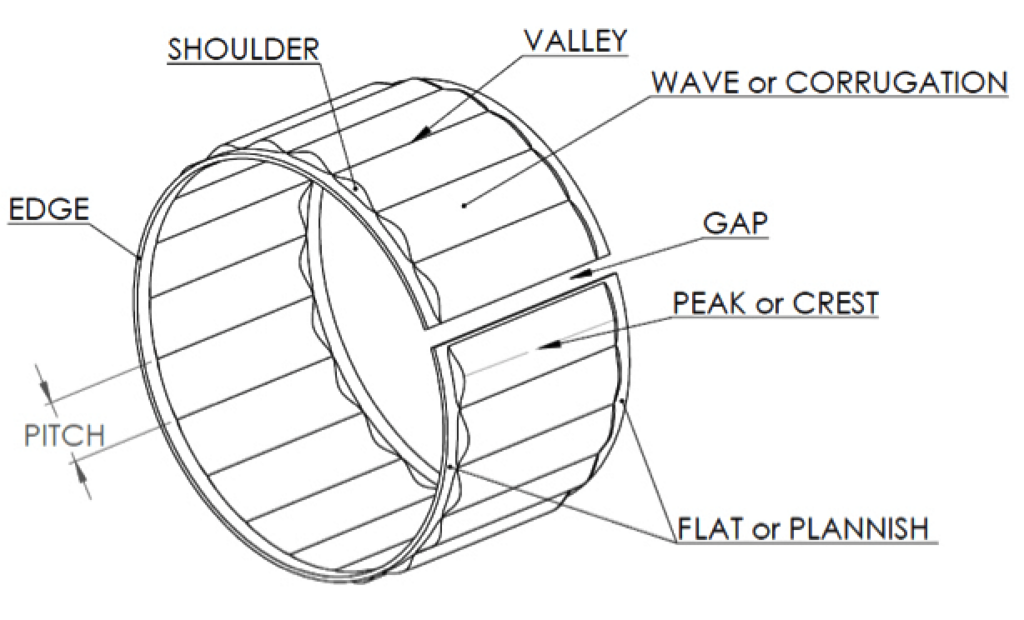
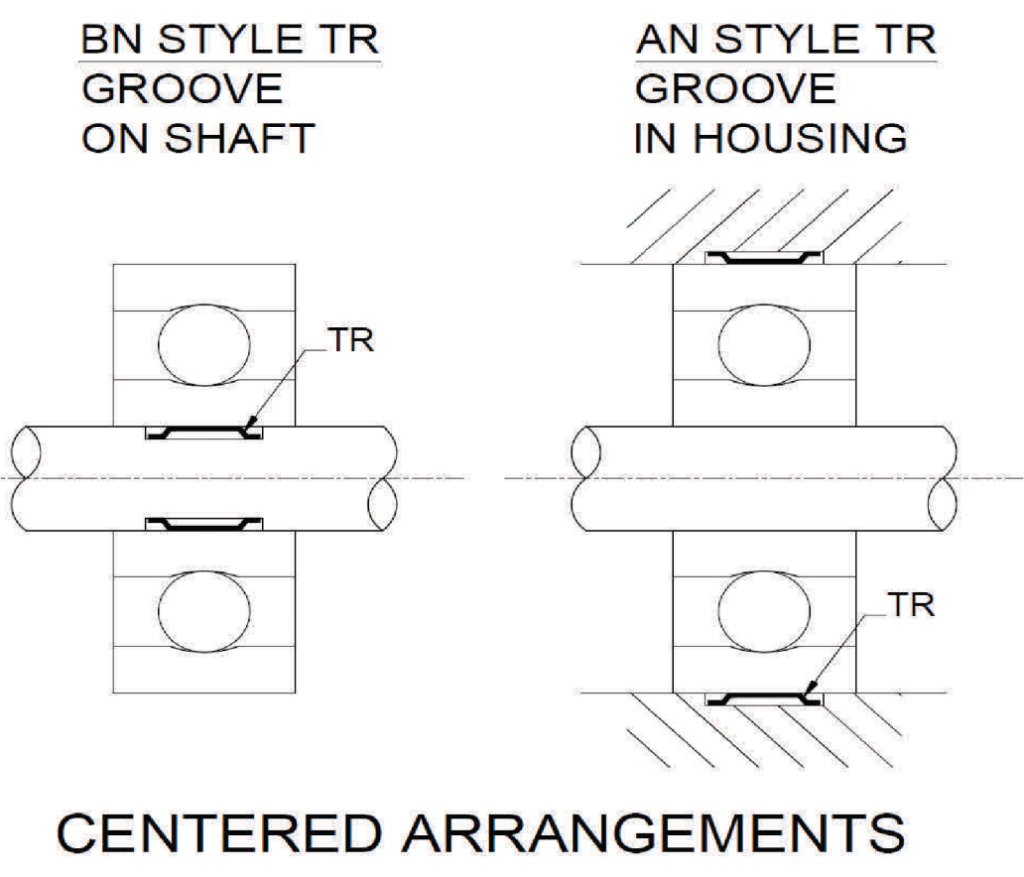
For cyclical loading, when possible, a high degree (typically 8% to 12%) of initial wave compression and a safety design factor of at least two is recommended. This calls for selecting a tolerance ring with a radial capacity that is at least double the maximum cyclical load. Selecting a tolerance ring that is narrower than the bearing and axially locating it within a groove will allow for handling radial loads that are greater than the radial capacity of the tolerance ring.
This is referred to as a “centered” arrangement and it requires the diameter on either side of the groove to be as close as possible to the diameter of the other component. A centered arrangement is prudent for successful applications of mounting shafts to bearing inside diameters or for cyclical loading applications.
Reducing Noise and Vibration on Rotating Devices
Noise and vibration can be detrimental to rotating devices due to excessive wear, structural fatigue, and energy loss. A tolerance ring’s spring-like characteristics can be used to reduce noise and vibration by shifting and changing the vibrational harmonics of mounted bearings. By shifting a bearing’s harmonics away from the natural frequency of the system, resonance can be minimized or prevented. The study and prediction of how a particular tolerance ring configuration will affect noise and vibration can be complex and is beyond the scope of this page.
Since there are several influencers in mechanical systems, experimenting with tolerance rings of varying stiffness (spring rate) is the best way to find the optimum harmonics shift. In some instances, tolerance rings may actually increase noise and vibration if they shift the bearing harmonics closer to the natural frequency of the system. If this occurs, experimenting with tolerance rings of different spring rates is the recommended approach.
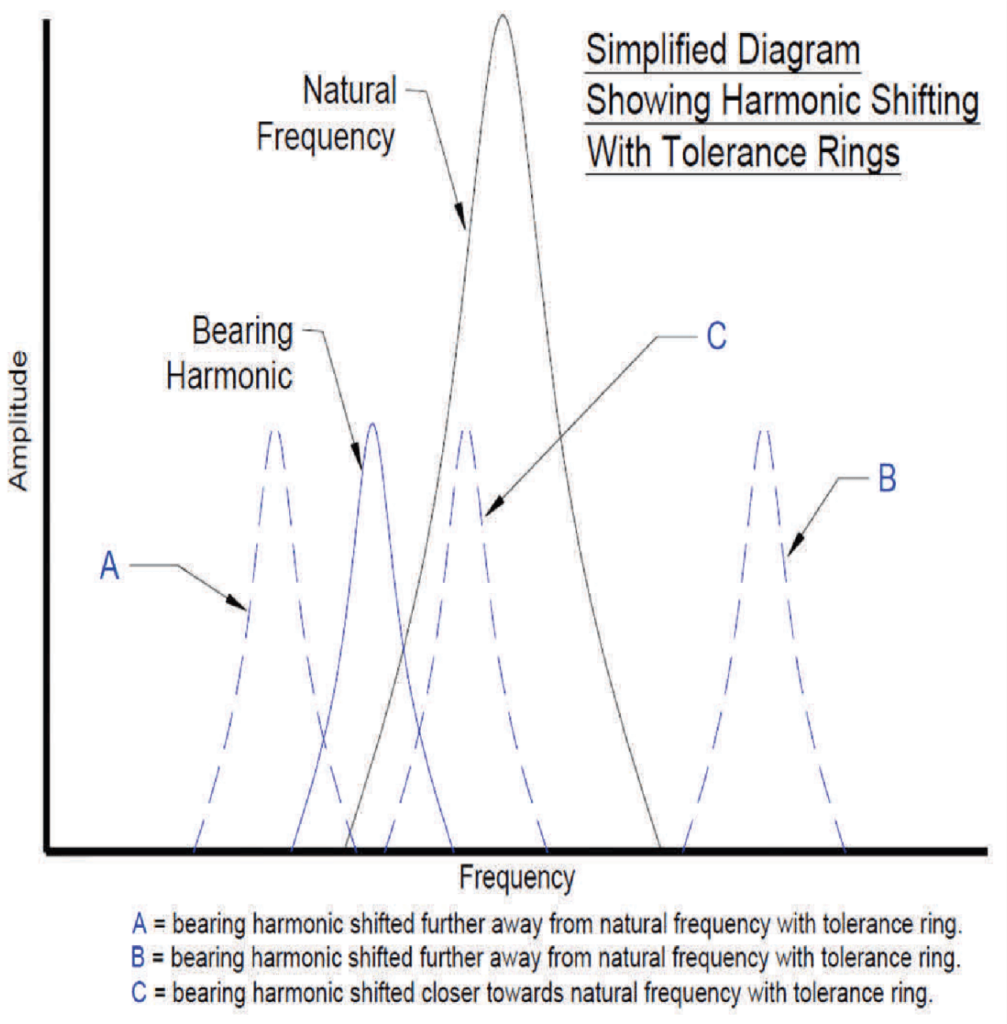
Compensating for Ball Bearing Misalignment Due to Misalignment
When press fit bearing pairs are misaligned due to non-collinear housing and bore hole center axes, additional radial loads, moments and vibrational forces are exerted on the shaft and bearings. If the misalignment is significant, bearings will fail prematurely.
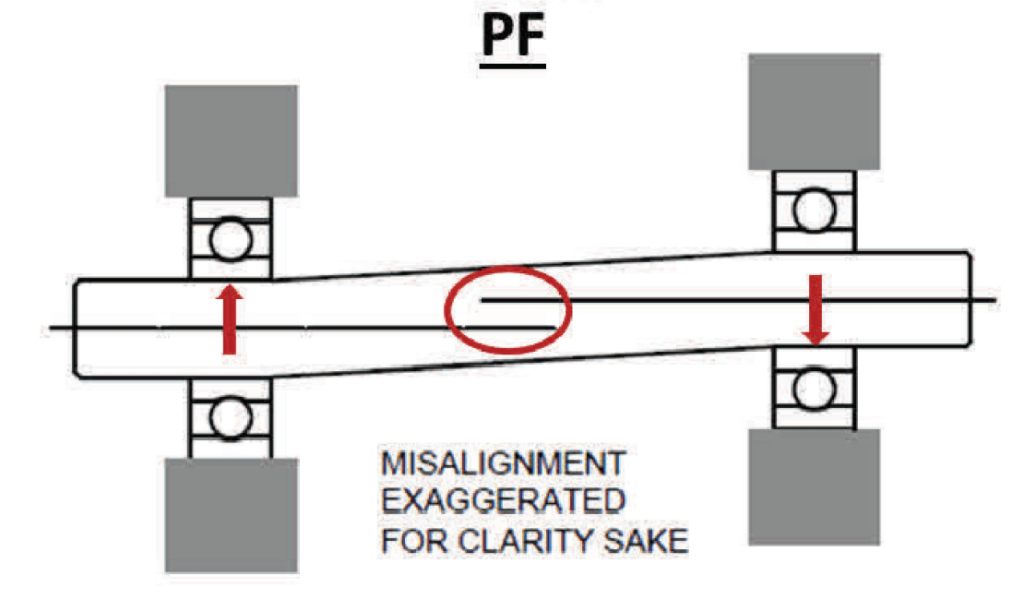
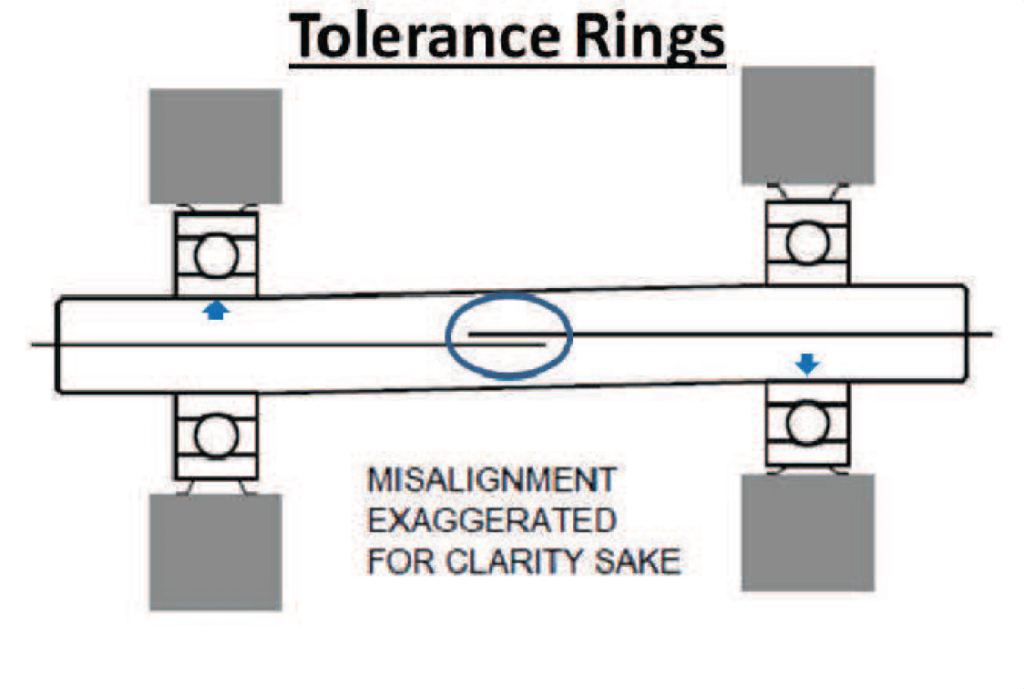
The waves of a tolerance ring are more forgiving than a press fit. Depending on the spring rate of the tolerance ring and amount of center axes offset, the wave’s spring-like characteristics will allow for improved alignment and longer bearing life.
Use our tolerance ring/bearing matching tool to match a standard tolerance ring to 42 common ball bearing sizes.
How Tolerance Rings Load into Applications
Tolerance rings have been used successfully with many applications involving preload washers and springs. The precise behavior is rather intricate, and each scenario depends on the assembly methodology and the component properties.
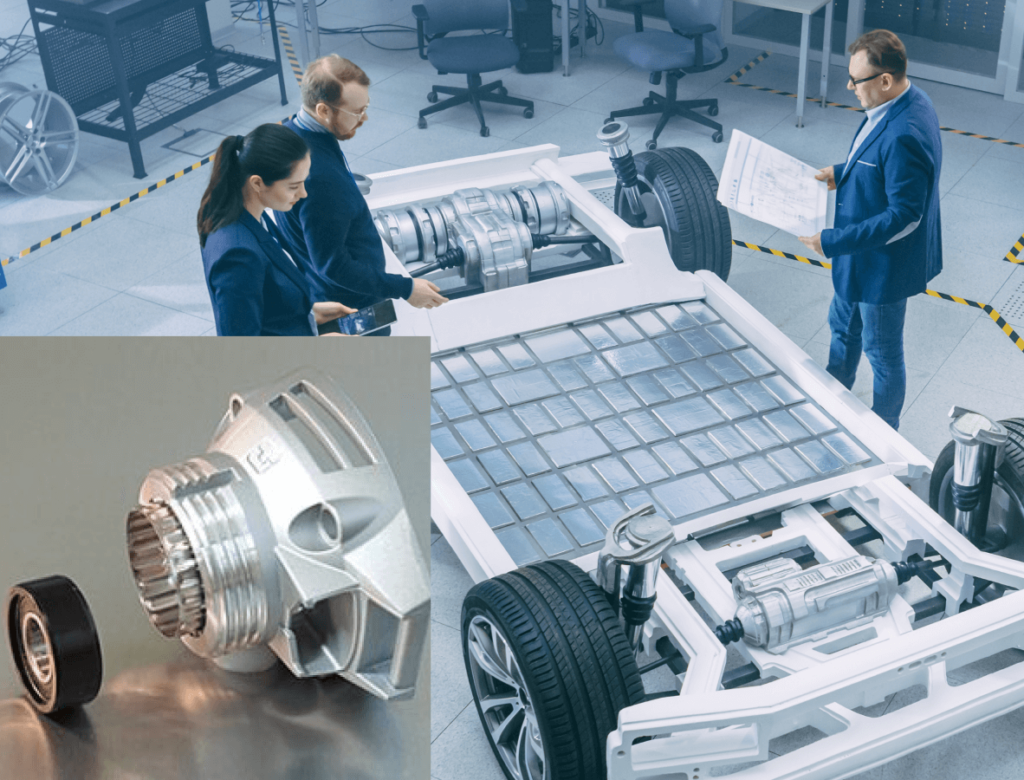
Typical influencing factors include the spring rate of the preload device, the encountered axial thermal strain, axial strength of the raceway ball contact surfaces, and thermal diametric growth/contraction occurring between components. Quantifying these values, however, is difficult due to the relational complexity of the component’s interactions.
Therefore, testing should be performed to confirm that a selected tolerance ring is working in conjunction with the preload device. When axial thermal growth and contraction occurs, the objective is to incorporate a tolerance ring that allows for axial slippage (a.k.a. float) prior to exceeding the axial load design limits of the ball bearing(s).
What are Tolerance Rings Made of?
Tolerance rings are typically made of 301 stainless steel (SST) or hardened carbon steel. The 301 SST provides good corrosion resistance while the hardened carbon steel can provide greater spring rates and radial capacities. The spring like properties of 301 SST is stable up to 450°F and the hardened carbon steel is stable up to 250°F. For applications calling for softer material, 316/316L SST can be used. Other exotic materials are available for extreme temperature applications such as Hastelloy® C-276 and Monel® K-500.
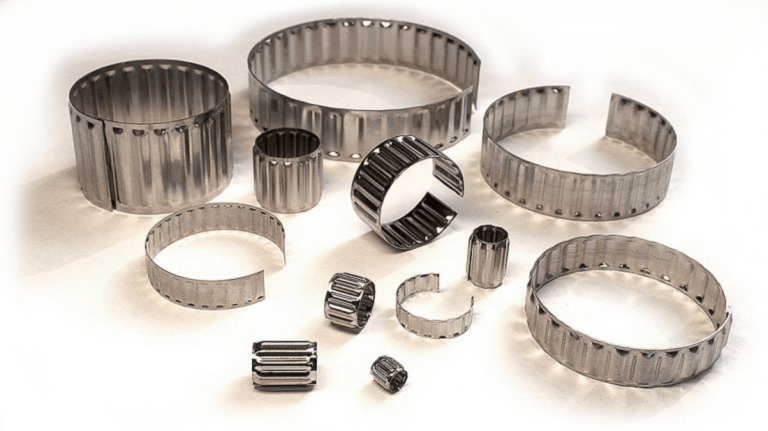
WHITE PAPER:
Technical White Paper on Tolerance Rings
Download the white paper to learn more about how tolerance rings are the superior choice to a press fit within applications.
Want to learn how tolerance rings can work for you?
Ready to get started?
Start a New Project